Injection molding plays a pivotal role in product prototyping, enabling the rapid creation of detailed and precise parts. This versatile process is essential in various industries, offering cost-effective and scalable production solutions. Among its various methods, reaction injection molding stands out for its unique advantages and applications. In this article, we will delve into the specifics of reaction injection molding (RIM), exploring its differences from traditional rubber injection molding, the materials commonly used, and its diverse applications.
Differences Between Reaction Injection Molding and Ordinary Injection Molding
Reaction injection molding differs significantly from traditional injection molding. Here are the key differences:
- Material State: RIM uses liquid polymers, while traditional injection molding typically uses melted thermoplastics.
- Pressure and Temperature: RIM operates at lower pressure and room temperature, whereas traditional injection molding requires high pressure and temperature.
- Cycle Time: RIM generally has a longer cycle time due to the curing process, while traditional injection molding is faster.
- Part Size and Complexity: RIM is ideal for large, complex parts with varying wall thicknesses. Traditional injection molding is better suited for smaller, uniform parts.
Working Procedure of Reaction Injection Molding
- Mixing: Two liquid components, typically polyol and isocyanate, are mixed at high pressure.
- Injection: The mixture is injected into a mold at low pressure.
- Curing: The material undergoes polymerization, solidifying within the mold.
- Ejection: The completed part is ejected from the mold after curing.
Common Materials Used in Reaction Injection Molding
Reaction injection molding majorly utilizes 3 kinds of materials, each with unique properties:
- Elastomeric Polyurethanes & Polyurethane Foam: Flexible, durable, and resistant to impact.
- Polyesters: Strong, heat-resistant, and versatile.
- Nylon 6: High mechanical strength, excellent wear resistance.
Typical Applications of Reaction Injection Molding
RIM is widely used across various industries due to its versatility and efficiency. Here are some typical applications:
- Automotive Parts
- Applications: Bumpers, dashboards, and exterior panels
- Advantage: RIM allows for the production of large, lightweight, and durable components. The process accommodates complex shapes and varying wall thicknesses, which is essential for automotive design.
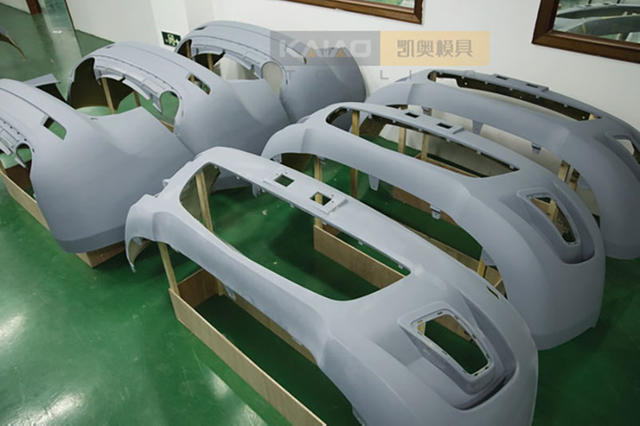
- Sports Products
- Applications: Helmets, protective gear, and equipment casings
- Advantages: The flexibility and strength of materials like elastomeric polyurethanes make RIM ideal for sports products that require high-impact resistance and durability.
- Architecture
- Applications: Decorative panels, structural components, and insulation.
- Advantages: RIM provides the ability to create intricate designs and large parts with excellent surface finishes. The materials used can also offer thermal insulation properties, making them suitable for architectural applications.
KAIAO’s Reaction Injection Molding Service
We, KAIAO, are one of the leaders in the realm of reaction injection molding, offering professional and efficient RIM services to meet diverse manufacturing needs. Our RIM process involves mixing and injecting polyurethane materials into molds, which are then cured through polymerization at low pressure and room temperature. This method ensures high efficiency, short cycles, and low-cost production runs, making KAIAO a trusted manufacturer globally.
Advantages of KAIAO’s RIM Service
- Large Parts Production: Capable of producing very large parts due to the properties of liquid polyurethane components
- Encapsulation of Inserts: Various inserts can be encapsulated during the molding process
- Flexibility in Wall Thickness: Design parts with significant wall thickness variations
- Class-A Surfaces: Produce parts with high-quality surface finishes suitable for painting
- Low-Cost Tooling: Low injection pressures allow for quicker and more cost-effective tooling compared to traditional methods
- Instant Quotes: Get quick quotes for orders ranging from 1 to 1,000 units per CAD
- Flexible Lead Times: Deliveries can be as fast as five days
- Precision and Quality: Tolerances down to ±0.0003’’ (0.010 mm) and compliance with ISO 2768 Medium, ISO 9001, AS 9100, and ISO 13485 standards
- Accurate Thickness Control: wall thicknesses ranging from 3 to 6 mm, providing high rigidity and strength. Despite the thin walls, the parts maintain excellent stability and durability
Our KAIAO’s reaction injection molding services combine simplicity, efficiency, and flexibility, making them the go-to choice for rapid injection molding and production. Our expertise and commitment to quality are for our clients, who can receive the best solutions tailored to their specific needs.
Conclusion
Reaction injection molding is a versatile and efficient method for producing high-quality, complex parts. It offers significant advantages over traditional injection molding, including lower pressure and temperature requirements, the ability to produce large parts, and flexibility in wall thickness. Common materials like elastomeric polyurethanes, polyesters, and Nylon 6 are used in various applications such as automotive parts, sports products, and architectural components.

And we, KAIAO, stand out in the industry and can satisfy your needs because of our high-standard injection molding factory, making us a reliable partner for your reaction injection molding needs. So, your businesses can achieve superior prototyping and production outcomes. Collaborate with KAIAO for your next project and experience the benefits of their top-notch services and contact us today!